Next in our three-part series exploring environmental sustainability across the coffee industry, we shift the focus to carbon reduction solutions in coffee roasteries. Catch up on
part one here
Roasting accounts for around 15% of coffee supply chain carbon emissions | Photo credit: Cottonbro
Cutting carbon at roasteries
After cultivation and transportation, roasting is the next significant contributor to coffee’s carbon footprint – accounting for around 15% of supply chain emissions. However, in Norway, one roaster has realised a bold vision for the future.
Founded in 1866, Joh. Johannson Kaffe accounts for around 50% of the coffee consumed in Norway – around 12,000 tons of roasted coffee per year. In mid-2020, the company fired up its new 465sq m
state-of-the-art roastery.
Through a combination of sustainable building materials, renewable energy generation and efficient design, the new building emits 85% less CO
2 compared to a conventional roastery.
“To reduce our carbon footprint as much as possible we needed to get the construction right as you can’t undo it later,” says Joh. Johannson Kaffe Production Director Bengt Ove Hagen.
“We decided to dive deep into the production process itself to conserve energy”
– Bengt Ove Hagen, Production Director, Joh. Johannson Kaffe
With timber storing approximately one ton of CO
2 per square metre of material used, using wood for 90% of the building’s construction in place of steel or concrete set the building up for big carbon savings. An array of 1,280 solar panels also enables the facility to produce around 15% of the energy required for operation.
“We decided to dive deep into the production process itself to conserve energy,” says Hagen. “Energy was one of the main emitters of carbon. We used propane in the old facility, but now we’ve switched to biogas. Using methane from non-fossil fuel sources has reduced our carbon footprint hugely.”
With low-carbon fuel in place, Joh. Johannson Kaffe turned to technology specialists Bühler Group to develop a more efficient method of roasting. Roasting accounts for more than 70% of the building’s energy usage. The ‘Infinity Roast’ system has delivered energy savings of up to 30% through a heat recovery system that stores and reuses excess energy that would otherwise be ventilated, to pre-heat coffee beans and provide heating for the building.
These operational efficiencies, however, do not come cheap, with the new roastery costing around 50% more than a comparable conventional operation. Nevertheless, Hagen is adamant the investment in the environment makes long-term business sense.
“There’s a business case of course – we wouldn’t be allowed to invest this much money if there wasn’t. Our owners think long-term and they really take climate change seriously,” he says.
The Bellwether Roaster in action. The fridge-sized electric roaster can be installed directly within coffee shops | Photo credit: Bellwether Coffee
UK-based Matthew Algie is another scaled coffee roaster taking a long-term approach to balancing sustainable supply chains and business needs. A pioneer of ethical and environmental initiatives in the coffee industry, the company was the first roaster to introduce Fairtrade espresso to the UK and the first in the world to offer triple-certified coffee.
In 2019, it became the
first roaster in the world to achieve the
Carbon Neutral International Standard, offsetting emissions by purchasing certified credits from a tree planting initiative in Uruguay and a wind energy project in India. By 2022, the company will contribute Fairtrade Premiums worth £1.5m ($1.8m) to help coffee farmers adapt to the climate emergency.
“Carbon reduction projects must be win-win – we need to reduce our footprint and see a business benefit at the same time,” says the company’s Managing Director, Ewan Reid.
While carbon credits can be a valuable tool to offset emissions, Reid asserts they should not be viewed as a magic bullet solution. “Offsetting is part of the solution but it’s a short-term approach. Relying entirely on carbon offset rather than carbon reduction is not sustainable,” he says.
In that spirit, the company continually optimises efficiency across its operation, whether through fine tuning the roasting schedules, installing LED lighting, or reducing air conditioning usage, all of which reduce energy consumption and costs.
“Over time our economy will be shaped by the true environmental impact of goods and services that we buy. In the long-term, our business will be more sustainable and more profitable going forward,” says Reid.
"We need to reduce our footprint and see a business benefit at the same time"
– Ewan Reid, Managing Director, Matthew Algie
With burning gas one of the most carbon intensive activities in coffee roasteries. US-based Bellwether Coffee is proposing a radical new approach. In 2019 the company launched
The Bellwether Roaster, a fridge-sized coffee roaster that can be installed directly within coffee shops and hospitality venues. Compared to a comparable gas-fired roaster Bellweather says its unit produces 98% fewer CO2 emissions.
“It’s very simple, very automated and the cool thing is that it really increases accessibility as people don’t have to be expert roasters,” says the company’s Head of Sustainability, Grayson Caldwell.
The system could allow direct oversight of carbon emissions from coffee roasting and reduce reliance on certification. In fact, Caldwell envisages a future where coffee roasting becomes far more decentralised, with coffee shops producing small custom batches.
The potential for electric roasting is clear. Bellwether’s annual sustainability report states the company’s fleet of US roasters saved 406.5 tons of carbon emissions in 2020 – equivalent to keeping a car off the road for 985,706 miles or turning off electricity in 90 homes for a year.
In the final part of the series we'll uncover the carbon footprint in coffee shops and ask what operators can do to reduce their impact. For more on carbon reduction solutions in roasteries, tune in to our podcast epiosde: The carbon footprint of coffee roasting
This article was first published in Issue 8 of 5THWAVE magazine.
Subscribe to 5THWAVE to receive each edition in print and digitally or sign up to our newsletter and be the first to read the latest articles and updates on World Coffee Portal research
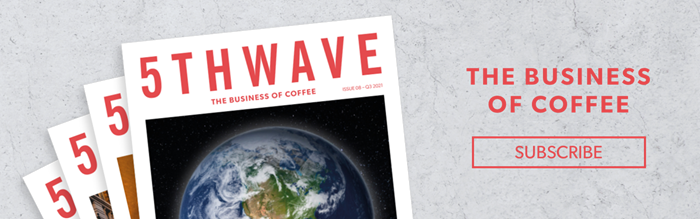